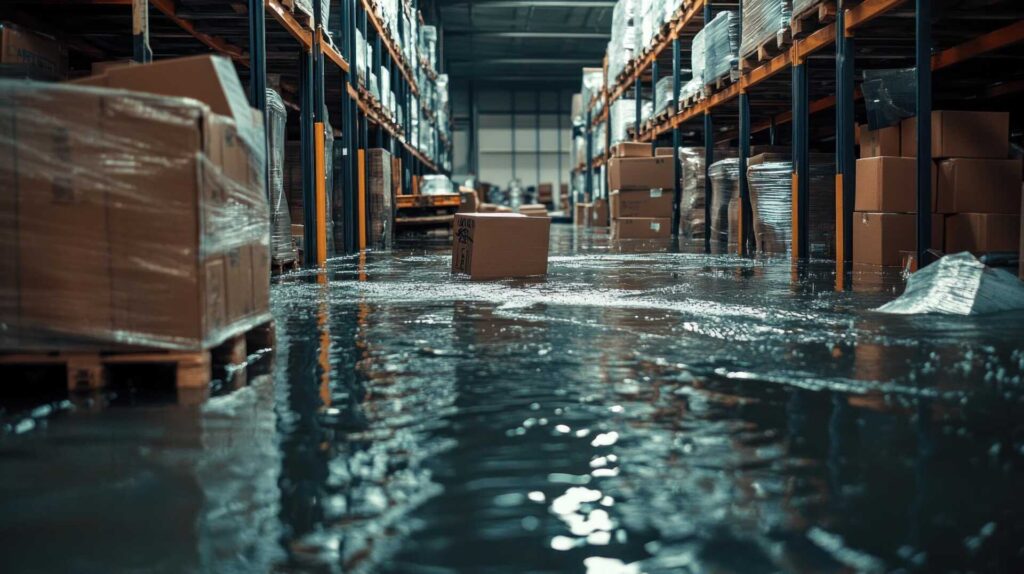
Contents
Did you know that many businesses do not reopen after a devastating flood event? As a business owner, you’re faced with numerous challenges following such disasters, but selecting the right flood restoration and cleanup strategy can be pivotal. From high-capacity pumps that efficiently remove water to advanced dehumidifiers that tackle lingering moisture, your choices in these initial steps are critical. You might wonder how these methods stack up against each other and which ones offer the best balance of speed and thoroughness to get your operations back on track quickly and safely. Let’s explore what makes each option advantageous and perhaps find the perfect fit for your situation.
Key Takeaways
- Utilize high-capacity pumps and submersible models for effective water extraction in flooded areas.
- Implement industrial-grade dehumidifiers and air movers to accelerate drying and prevent mold growth.
- Apply EPA-approved disinfectants to cleanse all surfaces and prevent pathogen spread.
- Engage professional restoration services for thorough damage assessment, documentation, and compliance with safety standards.
- Adopt preventive measures such as flood barriers and routine maintenance checks to mitigate future flooding risks.
Assessing the Damage Extent
Evaluating the full scope of damage is your first critical step in industrial flood restoration. When you’re dealing with the aftermath of a flood, understanding the extent of what’s been affected is crucial for a swift recovery, and for dealing with insurance claims effectively.
You’re not alone in this; every affected business is going through similar challenges, and sharing this common ground can foster a sense of community and support.
Start by conducting a thorough walkthrough of the premises. You’ll want to document all areas impacted by water, noting down the obvious signs of damage and looking for more subtle indicators such as water stains and odors that could hint at hidden issues.
It’s vital that you’re as detailed as possible—your insurance company will rely on this information to process your claim, and any missed details could mean a loss in coverage.
Next, categorize the damage into structural and non-structural. Structural damage will impact the integrity of your building, while non-structural damage generally involves contents and furnishings.
This distinction is important for both repair strategies and insurance purposes.
Water Extraction Techniques
Once you’ve assessed the damage, the next critical step is water extraction. This is where you’ll confront the challenge head-on, ensuring your space returns to its pre-flood condition efficiently. It’s crucial to select the right techniques that best fit the severity and nature of the flooding in your industrial setting.
Water extraction primarily involves two key approaches: pumping methods and drainage systems. Each technique has its strengths and is suitable for different scenarios. Let’s break down these options to help you make an informed decision.
Pumping methods are generally ideal for situations where water levels are high. Submersible pumps and gas-powered pumps are commonly used to remove large volumes of water quickly. They are powerful and can handle varying levels of water and debris without clogging. This method helps prevent prolonged exposure to moisture that could lead to structural damage.
Drainage systems, on the other hand, are effective for managing lower levels of water. These systems can be temporarily enhanced with additional sump pumps or integrated into existing infrastructure to improve water flow away from your property. They are especially useful in areas prone to flooding, providing a more permanent solution to water management.
Here’s a quick reference guide to help you understand these techniques:
Technique | Suitability | Benefits |
---|---|---|
Pumping Methods | High water levels | Fast, handles debris well |
Drainage Systems | Recurring water issues | Long-term solution, less labor |
Choosing the right water extraction method restores your space and reinforces a sense of security and continuity within your industrial community, ensuring everyone feels supported and prepared for future incidents.
Dehumidification and Drying
After successfully extracting the water, your next step is to focus on dehumidification and drying. This phase is crucial to stabilize the environment and prevent further damage to your property. You’re part of a community aiming to restore safety and functionality to spaces impacted by floods, and understanding the right techniques and tools is essential for effective recovery.
Start by selecting the appropriate restoration equipment. Industrial-grade dehumidifiers and air movers are key to promoting fast and efficient drying. These units work by pulling in moist air and expelling dry air, significantly speeding up the drying process of walls, floors, and furnishings.
It’s important to strategically place these devices throughout the affected area to ensure optimal coverage and air circulation.
Monitoring air quality during this phase is also vital. High humidity levels can lead to secondary damage, such as swelling of structural materials and fostering an environment conducive to mold growth.
Use hygrometers to monitor humidity levels and adjust equipment settings accordingly. This proactive approach preserves the integrity of the building and protects the health of its occupants.
Disinfection and Mold Remediation
While dehumidification and drying set the stage for a safer environment, the critical task of disinfection and mold remediation can’t be overlooked. After a flood, it’s crucial that you tackle these steps promptly to prevent further damage and ensure the health and safety of everyone involved.
First, let’s talk about disinfection. Floodwaters often contain hazardous substances, including bacteria and viruses. To address this, you’ll need to use EPA-approved disinfectants. Apply these meticulously across all affected surfaces. Remember, it’s not just about splashing the chemical around; you need to follow the recommended contact times to kill harmful pathogens effectively.
Next, mold remediation is equally vital. Mold can start to grow within 24 to 48 hours in moist conditions. Left unchecked, it poses serious health risks, especially in industrial settings where the scale of infestation can be vast.
Start by removing any wet items and materials that are mold-infested and can’t be adequately cleaned. For non-porous surfaces, cleaning with water and detergent might suffice, but often, specialized antimicrobial treatments are necessary to ensure spores are eradicated.
Throughout this process, adhering to health regulations is non-negotiable. These rules are designed to protect you and your team’s health, and they provide a framework for effective cleanup that meets safety standards.
Additionally, implementing preventive measures like ensuring good ventilation and maintaining low humidity can help stop mold from recurring.
Your role in this isn’t just about restoration; it’s about fostering a safe and healthy workplace that stands resilient against future challenges.
Structural and Content Restoration
Moving beyond initial cleanup, it’s essential to focus on structural and content restoration to bring your industrial facility back to full operation. Ensuring the structural integrity of your building is paramount for the safety and longevity of your facility. You’re not alone in this—you’re part of a community that values resilience and recovery.
Content salvage involves meticulous attention to damaged items within your facility. Whether it’s machinery, documents, or furnishings, each item requires a specific approach tailored to its material and the extent of damage. Here’s a practical guide to help you understand the process:
Process | Description | Example |
---|---|---|
Inspection | Assess structural damage and item conditions. | Checking support beams for integrity. |
Cleaning | Thorough cleaning of all salvageable items. | Using specialized solutions on machinery. |
Restoration | Repairing or replacing damaged structural parts. | Replacing corroded pipes. |
Dehumidification | Removing moisture to prevent further damage. | Industrial-grade dehumidifiers in operation. |
Final Assessment | Ensuring everything is restored to safety codes. | Final walkthrough with a structural engineer. |
Focus on each step methodically to ensure that no aspect of your restoration process is overlooked. It’s crucial to work with professionals who understand the complexities of industrial recovery. They’ll help ensure your facility isn’t just restored and improved where possible.
Wrap-Up
So, you’ve weathered the storm, but now your industrial space looks like a swamp scene from a budget apocalypse movie. Fear not! Employ these top-notch flood restoration tactics: suck up that swamp with high-powered pumps, zap moisture with industrial dehumidifiers, scrub away the creepy-crawlies with EPA-approved disinfectants, banish mold to the shadow realm, and patch up your premises and gear. Get cracking, restore your empire, and show that flood who’s the boss of this concrete jungle!
Recent Posts
What Are Emergency Water Removal Services?
Imagine water pooling in your living room, threatening to damage your cherished belongings and compromise
How to Remove Water From Flooded Basements
Flooded basements affect nearly 14 million homes in the U.S. each year, making effective water
Your Guide to 24/7 Emergency Water Damage Repair
Did you know that the initial 48 hours after water damage are critical in preventing