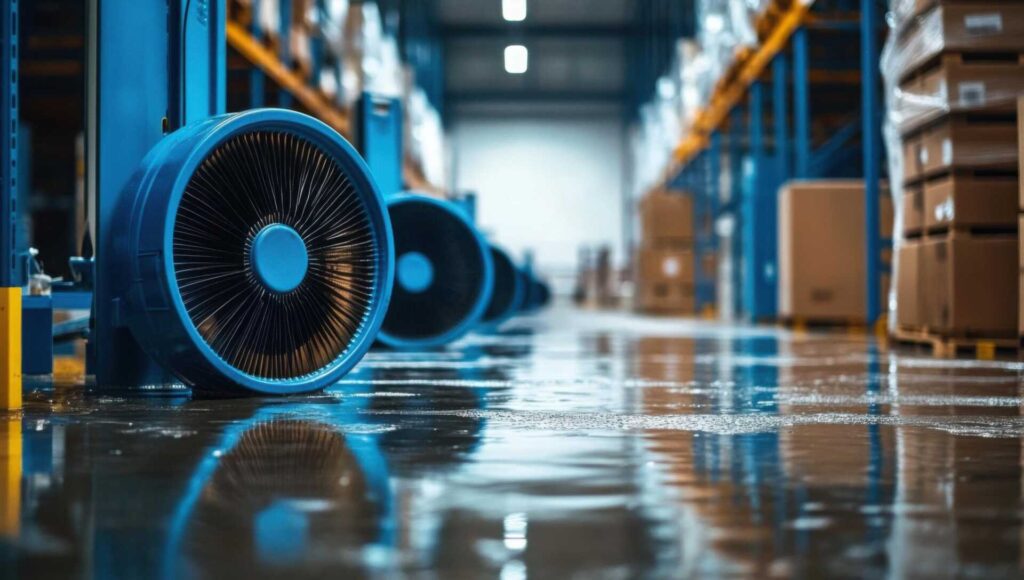
Contents
When you’re facing the aftermath of a flood restoration in your industrial space, it’s crucial to act swiftly but carefully to minimize long-term damage and downtime. First, you’ll need to categorize the water to gauge contamination levels—this step will dictate the safety measures and cleanup methods you’ll employ. After water extraction, which should be done using powerful pumps, you’ll move on to drying and dehumidifying the vast areas affected. However, the real challenge often lies in the details, such as ensuring your machinery and electrical systems are dry, fully functional, and safe to operate. What happens if these components aren’t properly restored? Let’s explore the potential risks and the strategies to mitigate them.
Key Takeaways
- Employ powerful pumps and enhanced drainage systems to efficiently remove high volumes of water from affected areas.
- Utilize industrial-grade dehumidifiers and strategic ventilation to rapidly reduce humidity and dry the facility thoroughly.
- Apply EPA-approved disinfectants using sprayers or foggers to sanitize all surfaces exposed to floodwater, ensuring a clean environment.
- Conduct detailed inspections and restore damaged machinery, prioritizing critical equipment to minimize operational downtime.
- Implement continuous monitoring with hygrometers to maintain optimal humidity levels and prevent mold growth.
Assessing Water Damage Severity
Before assessing the severity of water damage in industrial spaces, it’s crucial to understand the specific characteristics of the water involved. You need to consider the source of water, whether it’s clean water, gray water, or black water, as this will significantly influence your damage assessment process. Knowing the type of water helps determine the potential contaminants and the urgency of the response needed.
As you evaluate the severity of water damage, you’ll first focus on visual indicators. Look for water lines on walls which can tell how high the water reached. Check for signs of mold and mildew, as these can point to prolonged exposure to moisture, a critical severity indicator.
Don’t overlook materials; water affects different substances in diverse ways. For instance, drywall absorbs water quickly and can become a structural concern, while metal might be more resilient but prone to corrosion.
Your next step is to assess the operational impact. How has the water affected your machinery and equipment? This is vital because any downtime directly translates into financial loss.
Electrical systems are particularly susceptible to water damage. Ensure you assess these comprehensively, as failures here can be both costly and dangerous.
Water Extraction Techniques
Once you’ve assessed the severity of water damage in your industrial space, the next crucial step is to begin extracting the water efficiently. You’re not alone in this; every industrial manager faces this challenge, and finding the right water extraction techniques is vital.
Utilizing powerful pump systems is your starting point. These systems are specifically designed to handle high volumes of water, making them ideal for large areas affected by flooding. It’s essential to choose a pump with sufficient capacity to manage the volume of water in your space to speed up the extraction process.
Next, consider your drainage solutions. Effective drainage is critical in preventing further damage and expediting the water removal process. You’ll need to ensure that your existing drainage system can handle the increased flow or consider temporary enhancements to cope with the additional load.
Here’s a practical guide to help you select the appropriate techniques and equipment:
Technique | Equipment Type | Considerations |
---|---|---|
High-Volume Pumping | Submersible Pumps | Choose based on water level and volume |
Directed Water Flow | Portable Sump Pumps | Ensure mobility for targeted extraction |
Enhanced Drainage | Industrial Drain Mods | Temporary or permanent modifications |
Strategic Placement | Wet Vacuums | Use for hard-to-reach areas and cleanup |
Drying and Dehumidification Processes
After successfully extracting the bulk of the water, it’s crucial to initiate the drying and dehumidification processes to prevent mold growth and further deterioration of your industrial space.
You’re not alone in facing these challenges, and focusing on precise humidity control and effective ventilation techniques will help you restore your workspace efficiently.
First, assess the overall humidity levels using hygrometers or moisture meters. It’s essential to achieve a balance where the air is dry enough to thwart mold formation but not so dry that it damages materials or machinery. Aim for a relative humidity level between 30% and 50%.
Industrial-grade dehumidifiers are your best allies here, capable of handling large volumes of air and reducing humidity rapidly.
Next, integrate strategic ventilation techniques. Proper airflow is critical in speeding up the drying process. Use industrial fans to circulate air throughout the affected areas.
Position these fans at key points to ensure a thorough exchange of moist inside air with drier outside air. If the outdoor air is more humid, consider using HVAC systems to treat the air before it circulates back into the space.
Remember, every component of your industrial space, from the floors to the high ceilings, needs attention.
Specialized equipment like high-volume air movers can target these hard-to-reach spaces, ensuring that moisture isn’t lurking anywhere.
Sanitizing Contaminated Areas
Following the drying and dehumidification of your industrial space, it’s crucial to sanitize areas that were exposed to water to prevent any health hazards or further contamination. The first step in this process is identifying all surfaces that came into contact with floodwater. This includes walls, floors, and any stationary equipment not discussed in the subsequent section on equipment restoration.
To begin, you’ll need to choose the appropriate chemical treatments. These are vital in combating mold and ensuring mold prevention. Opt for EPA-approved disinfectants that are effective against a broad spectrum of bacteria and viruses. Apply these treatments using either a sprayer or a fogger to ensure thorough coverage, especially in hard-to-reach areas.
Next, focus on air quality. It’s not just surfaces that need attention; airborne pathogens can pose a significant risk, too. Use HEPA air scrubbers to filter out mold spores and other contaminants to ensure that the air in your facility is safe to breathe.
Remember, the goal here isn’t just to clean, but to create an environment that’s inhospitable to mold growth and bacteria. Regularly check humidity levels with hygrometers to maintain optimal conditions that discourage mold proliferation.
Lastly, document every step taken during the sanitation process. This documentation won’t only help in maintaining standards but also reassure your employees and stakeholders that the environment they’re returning to is safe and clean.
Restoring Damaged Industrial Equipment
Shifting your focus to the restoration of damaged industrial equipment, you’ll find that precision and a methodical approach are key to effective recovery.
Post-flood, the integrity of your machinery and equipment can significantly impact productivity and safety. It’s essential to prioritize equipment inspection and implement restoration techniques that bring your operations back to full capacity quickly and safely.
When tackling the restoration of your industrial equipment, consider these steps:
- Conduct Thorough Inspections: Immediately after a flood, inspect each piece of equipment for water ingress, signs of corrosion, or mechanical damage. Use moisture meters and other diagnostic tools to assess the extent of water damage. Documentation during this phase is crucial for insurance claims and future reference.
- Clean and Decontaminate: Remove all mud, debris, and contaminants from equipment using appropriate cleaning agents. Ensure that all parts, especially those that are hidden or less accessible, are thoroughly cleaned to prevent long-term damage and malfunctions.
- Dry and Dehumidify: Employ industrial-grade dehumidifiers and air movers to dry out equipment thoroughly. Pay special attention to electrical components and areas where moisture can remain trapped for extended periods.
- Restore or Replace Components: Assess whether components can be salvaged through precise restoration techniques or if they need replacement. Prioritize restoring critical machinery to minimize downtime.
Always test restored equipment extensively to ensure it operates safely before full-scale production resumes.
Final Thoughts
As you navigate the aftermath of a flood, think of your industrial space as a resilient ecosystem. Just as nature revitalizes after a storm, so too can your facilities. With precise damage assessments, robust extraction methods, and thorough drying techniques, you’ll restore balance. Sanitize diligently and inspect your machinery with a keen eye, ensuring every component thrives like new growth in a rejuvenated forest. Embrace these tactics as your blueprint for revival, and watch your industrial environment flourish once again.
Recent Posts
What Are Emergency Water Removal Services?
Imagine water pooling in your living room, threatening to damage your cherished belongings and compromise
How to Remove Water From Flooded Basements
Flooded basements affect nearly 14 million homes in the U.S. each year, making effective water
Your Guide to 24/7 Emergency Water Damage Repair
Did you know that the initial 48 hours after water damage are critical in preventing